The UK quattro Network
The UK's mobile Audi 5-cylinder mechanic - 07833 654800, 24x7
Specialist in turbos, quattros, electrics and non-starts
Rebuilding the tandem-style hydraulic pump
(This procedure does not apply to the earlier system using
ATF fluid as fitted to, e.g., WR and WX-engined ur-quattros)
This is the full procedure including the shaft seal. It is in general applicable to all tandem pumps such as the long "grey casting pump" ("Graugußpumpe") fitted to later Type 44s and the box-shaped pump fitted to the MB and RR ur-quattros, Audi S2 amongst other vehicles. Be aware that a leaking power steering pump is now an MoT failure item.
A degraded brake assist pump can cause poor brake performance. The classic test is to remove the drive belt (as described below) and rotate the pump with a finger pressed onto the outside of the pulley. There should be a marked resistance - twice per revolution on earlier pumps, only once on later models. It should be necessary to grip the pulley to overcome this.
Parts required:
- 1.5 litres of hydraulic oil - Audi part G 004 000 M2. More will be required for a self-levelling Type 44 because of the greater capacity of the square reservoir fitted to these cars
- Seal kit for pump as appropriate - varies by vehicle
- New crush washers or O-rings for pump lines as appropriate - varies by vehicle. Note that the superficially identical box-shaped pumps fitted to MBs and RRs are not interchangeable - the later RR and S2 pump uses recessed O-rings on its hose connections in contrast with the MB and MC-2's crush washers.
- New piston caps (X-caps) are available from Audi as p/n 026 145 541.
Special tools required:
- Impact driver with
- 16mm draglink socket (misnomer - actually a fat screwdriver) - e.g., FACOM ENS.316
- 4mm Allen impact bit
- MityVac with collecting bottle or long thin siphon tube
- Hydraulic ram puller (e.g., Sykes Pikavant 150000) - a mechanical screw type will NOT do
Otherwise it is assumed that a comprehensive toolbox is available. A digital camera is useful to record, e.g., the position of the mounting brackets on the pump prior to removal from the car.
Many people have only limited success at this operation - it is a Haynes "5-spanner" item. There is nothing intrinsically difficult - care and attention to detail will guarantee success. Cleanliness is important, as is an understanding of some of the basic principles of engineering. The pump is lubricated by the oil it pumps, so all references to "oil" on this page refer to green hydraulic oil; Audi part number G 004 000 M2 or an equivalent.
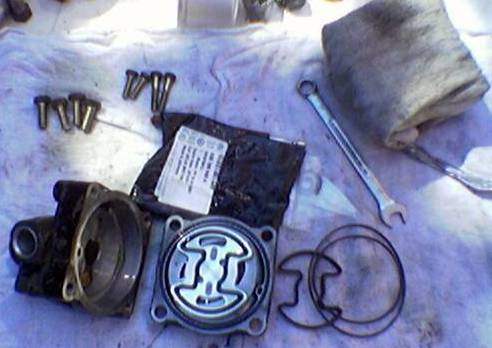
Audi hydraulic pump split showing
Rubber Seal from Hell - RSFH
The tandem pump is actually two pumps, as its name implies. The rear section is a standard high-volume low-pressure power steering vane pump - the front part is a low-volume high-pressure pump for the braking system fed by an internal bleed from the power steering pump. The hoses are - from front to back - high pressure to brakes, lower pressure to power steering, feed from the reservoir. The latter two are normal hoses and can be replaced with made-up patterns, but the high-pressure brake accumulator hose contains a special constrictor to reduce noise.
The rear half of the pump is essentially sealed and apart from some O-rings between itself and the front portion is along for the ride in the following procedure. It stays in one piece via stiction but can fall apart and scatter the vanes on the bench if not treated with respect. The front part is somewhat more stressed. Most rebuild failures occur because one of the mating faces is damaged or O-rings are not pre-oiled when being replaced. The following procedure is for complete disassembly to replace the shaft seal - note that in this case the pistons cannot be replaced until after the pump has been reassembled.
While the pump is split into two halves, it is VERY susceptible to damage; this procedure has been optimized to reduce this time. The central body joint is metal-to-metal and the slightest burr on an edge will prevent a good seal. This joint is under considerable pressure because of the pump-to-pump feed - if it leaks, check for this first. Otherwise, an extremely thin film of Loktite 542 thread sealant may help. Yes, that is how much 50ml costs. No, they don't make smaller bottles.
Procedure:
- Despite the precautions listed here, some spillage is inevitable both under the car and from the pump as it is handled, especially as it is turned over during removal. More oil will be released as each cap is undone - be prepared, this is a messy job. Carefully emptying the pump before starting disassembly is pointless as any given pump is never empty
- Pump the brakes to return as much hydraulic fluid as possible to the reservoir
- Drain the hydraulic reservoir using the MityVac or a siphon tube
- Optionally, the filter in the reservoir can be washed at this point. Pull it up until it stops right at the limit of its travel, grasp it in a fist and hit that fist from underneath with the other. Despite the noise, nothing has broken - use fuel or paraffin (kerosene) to wash the filter. The reservoir can be removed and washed, but care should be taken with the upper hose connection; no attempt should be made to undo the clip because it is always rusted beyond the point at which the plastic pipe can stand the undoing torque. It should simply be cut off with a hacksaw. After replacing the filter, a small magnet can be dropped in to collect any metal fragments appearing in the oil in the future
- Detach the rear hose from the pump and repeat the drainage operation for the pump's rear chamber. The thinner the hose used the better, because the pump must be rotated clockwise during removal and any oil left in this chamber will spill
- Detach the other hoses - the front one is also bolted to the rear of the pump - and pull them out of the way
- Loosen the pump pivot bolt
- Loosen the adjustment clamping nut on the bracket below the pump using a 13mm socket on an extension inserted from the dipstick area or a stubby 13mm ratchet spanner
- Wind out the tensioning bolt, leaving it just engaged in the tensioner below
- Remove the adjustment clamping nut (watch for the washer) and the adjuster
- Drop the belt off the pulley
- Remove the pivot bolt and the pump. On the MB and RR ur-quattros, the pivot bolt fouls the auxiliary radiator and the easiest solution is to remove the bracket
- Hold the pump in something like a Black and Decker Workmate or a workshop vice with wooden packing pieces
- Loosen the pulley bolts by bracing a large screwdriver between each bolt and the hub in turn and loosening one of the other bolts - an air impact wrench can also be used. When all bolts have been loosened, remove them all
- Using a broad cold chisel from behind between the trunnion and pulley, ease the pulley off the trunnion. Do NOT use a puller from the front as this will distort the pulley
- Remove the mounting brackets from the pump
- Note the separation between the trunnion and the shaft seal - heat-resistant packing to replicate this distance will be required later
- Using a hydraulic ram puller, remove the trunnion from the shaft. This is a very tight interference fit and a pull of up to 8 tonnes may be required. Be ready for a very loud report when it starts to move - children and animals within range may be alarmed
- Using the impact driver and draglink socket, remove all the large caps around the pump, noting carefully which way up the piston assemblies go and their locations - it is not intuitive
- Using the impact driver and 4mm Allen driver, remove the two smaller caps and their pistons. Take good care to clean out the Allen recesses in the caps - use relatively small but frequent taps on the impact driver. This may take time - it is easy to shear the driver
- As with cylinder head work, parts that have run together should be kept together. Wipe all parts with lightly-oiled kitchen roll
- Clean out the O-ring seats under the caps and the caps themselves. Toothpicks and cotton buds are useful
- Once all of the caps and pistons have been removed, the bolts holding the pump together may be removed. If these are Allen bolts (most "grey casting pumps") clean out the heads of the two Allen bolts on the rear of the pump that hold it together, hammer in an appropriate driver, and remove the Allen bolts. They may be extremely tight - extra care in inserting the driver will avoid having to resort to engineering to get them out. Some pumps have ordinary hex-head bolts
- Split the pump with the rear held uppermost and place the rear half face down on folded cloths or a soft surface. In the box-shaped pattern of pump, one seal looks like the result of a midnight assignation between a demented "H" and a drunken "Z". It is commonly referred to as "the rubber seal from hell" - RSFH - it has a "top" and "bottom" but is laterally symmetrical. Note carefully the up/down orientation of the old seal so that the new one can be inserted correctly
- Withdraw the shaft from the front end, taking care to ensure that the phosphor-bronze sleeve does not fall, and place the front end face down on folded cloths or a soft surface.
Take extreme care to ensure that neither the facing surfaces nor the edges are damaged in any way - wrap each half of the pump in rags and place it somewhere safe when working on the other half
- Carefully knock out the shaft seal from behind with a long punch
- Oil the new shaft seal and push it into place. If it is necessary to apply some light taps with a soft-faced hammer, place cloths under the mating face.
- Reassemble and oil the pump rotor and carefully reinsert it into the front half of the pump, checking that the shaft seal is lightly oiled around it
- Replace the internal O-rings, cleaning out each seat with a non-metal tool such as a toothpick or cotton bud
- Clean both mating faces of the pump using a clean, dry cloth leaving a coating of oil on the O-rings themselves
- Remate the halves of the pump, noting that all hose unions are on the same side
- Replace and tighten the bolts that hold the halves together
- Replace the pistons and their caps, ensuring that the pistons and the new O-rings are dipped in oil - dry O-rings will tear during tightening and are the major cause of failure in rebuilds after burring of the mating surfaces
- Hold the pump vertically in a vice with wooden packing pieces and protect the new shaft seal from heat with sufficient packing to replicate the original separation noted above. Have a large wet rag handy (in a washing up bowl or saucepan containing water) and wear thick gloves
- Heat the trunnion to red heat, wait for it to blacken again, and drop it on the shaft to rest on the packing. It may need to be tapped down very gently. Cool it as rapidly as possible using the wet rag, which will heat up VERY quickly to and beyond scalding
- Replace the mounting brackets and the pulley
- Remount the pump, filling the rear section of the pump with fresh oil before attaching the rear hose
- Refill the hydraulic reservoir with fresh oil and start the engine. Check the level after a few seconds and again once the steering has been turned lock-to-lock and the car has been driven a few miles
Kerbside Motors Home Page and Contact Information
Contact Phil Payne by email or use mobile/SMS 07833 654800