The UK quattro Network
The UK's mobile Audi 5-cylinder mechanic - 07833 654800, 24x7
Specialist in turbos, quattros, electrics and non-starts
Audi 10V I5 Turbo Engines - Cylinder Head Removal
(Does NOT apply to aluminium engines - refer to an authorized Audi dealership)
This text version has been converted to XHTML to support handheld browsers. There is also a pictorial version in development.
In the following discussion, "remove" means "undo, take off the car and store" - "detach" means "undo and leave on the car".
- [MB, WR, WX] Remove headlight trims, radiator grill
- [MB, WR, WX] If removeable transom fitted, detach end of bonnet release cable (7mm) and remove transom
- [MC, 1B] Remove radiator grill & intercooler
- Loosen hydraulic pump pivot bolt, slacken and remove adjuster, detach belt
- [WR, WX, MC, 1B] Remove hydraulic pump pivot bolt
- Remove bolts securing hydraulic pump bracket to head
- Tie hydraulic pump up out of the way
- Remove upper cambelt cover (2x 6mm Allen). Loosen and remove the lower nut first - if the upper stud comes out with its nut, it may be possible to catch the spacer behind the cover before it falls into the crank pulley area. See below for a tool recommendation
- Drain coolant
- Drain oil
- Remove [main] oil filter to drain head galleries.
- [MB, WR, WX] Remove auxiliary radiator (loosen but do not remove two 10mm nuts underneath - base of auxiliary radiator slides out of slots in bracket backwards)
- Remove injector cooling fan deflector
- [MB, MC, 1B] Detach upper end of crankcase breather pipe from union on cam cover
- Remove plug wires, plug wire shroud & distributor cap
- Pull off rotor arm, remove dust cap, replace rotor arm (for roughly locating TDC)
- Detach inlet hose from injector cooling fan on side of head
- Unplug & remove injector cooling fan
- Unplug Hall sensor (distributor)
- Remove spark plugs
- Unplug control pressure regulator, unscrew from side of block & place on metering head - fuel lines stay attached. A special tool is useful.
- Detach accelerator cable from throttle quadrant - two safety clips should be present
- Undo injector line clip on inner side of inlet manifold
- Detach accelerator cable bracket from top of inlet manifold and tie back, taking care not to kink the accelerator cable
- Unplug cold start injector, unscrew from manifold & place on metering head - same tool useful
- Pull out injectors using ViseGrips or similar to grip the injector and a large screwdriver as a lever - place on metering head
- [MB, WR, WX] Unplug fuel consumption potentiometer (side of metering head)
- [MB] Unplug fuel frequency valve (green, behind metering head)
- Unplug switch(s) on throttle body & cut any cable ties to metering head
- [MB, WR, WX] Loosely tie detached fuel pipes to metering head, undo fuel feed (two high-quality adjustables or flare nut wrenches recommended - the 14mm flare nut is very easily damaged) & return (slim 19mm open-ended required) lines, pull off breather hose, disconnect accordion hose, unclip air filter housing and lift out entire fuel injection system
- [MB, WR, WX] Wrap open fuel line ends in aluminium foil to prevent dirt entry.
- [MB, WR, WX] Remove air filter housing
- [MB, WR, WX] Remove accordion hose and plug turbo inlet with rags
- [MC, 1B] Remove air filter cover & air filter
- Loosen spark plugs
- Turn engine to TDC (cam/distributor) using #3036 on cam wheel, spanner on cam wheel bolt (19mm) or #2079 on harmonic balancer bolt (if car on lift)
- Lock crankshaft with tool #2084. Do NOT use transmission.
- Detach top coolant hose from radiator
- Loosen water pump & rotate to loosen cambelt
- Apply cable tie to cambelt below cam gear
- Break cam gear bolt loose (80Nm - tool #3036 highly recommended)
- Undo cable tie and pull cambelt off cam gear
- Pack space below cam gear with rags in case Woodruff key falls (use rag same way during reassembly)
- Remove cam gear bolt, cam gear & Woodruff key
- [MB] Unscrew turbo after-run water pump from side of block
- [MB, MC, 1B] Check pump impeller rotates when voltage applied. The pump contains a magnetic clutch - buzzing does not mean it's actually pumping
- [MB, WR, WX] Tie loose loom back to air filter housing bracket
- Remove crankcase & cam cover breathers
- Disconnect injector cooling fan thermoswitch & remove heatshield & coil grounding strap from rear of cam cover
- [WR, WX] Remove bell housing bolts holding wastegate support bracket(s) if present
- Remove right CV joint heat shield (from underneath car)
- Disconnect downpipe from centre exhaust section & gearbox mounting
- Using a 3/8ths drive 13mm six-point socket & a duct-taped universal joint, undo wastegate to downpipe nuts - assistant useful to hold bolts from above, preferably skilled. Access may be better through the right wheel well with the road wheel removed
- Detach both vacuum pipes from wastegate
- Unbolt wastegate from exhaust manifold & remove
- Undo turbo oil connections & tie upper oil line well out of way
- [MB, MC, 1B] Detach upper & lower turbo water pipes - lower pipe non-trivial - 15mm Crowfoot flare nut socket recommended
- [MB, MC, 1B] Detach bracket holding upper turbo water feed and cam belt backing plate to front lower side of head
- [WR, WX] Remove bolt securing cam belt cover backing plate to front lower side of cylinder head
- Detach exhaust downpipe from turbo & push aside - upper nut next to engine non-trivial; requires semi-deep socket on long extension. 72-click gimbal-head ratchet (e.g., FACOM J.159) recommended
- Detach turbo to intercooler hose from turbo
- Detach turbo from manifold & remove from car - lower right nut non-trivial.
(If assistant available, head can be lifted with turbo still attached - this is commonly done)
- Detach temperature sender wire, ECU vacuum feed & differential lock vacuum feed from rear of head & manifold
- [WR, WX] Remove pipe between wastegate centre chamber and exhaust manifold. Care required at manifold end - 19mm open-ended Crowfoot socket on very long extension through right headlight hole recommended. This pipe is an expensive part - significant care is appropriate. If in doubt, leave attached and remove on the bench
- [MB, MC, 1B] Detach wastegate main feed & wastegate control valve feed from rear of inlet manifold
- [MB, MC, 1B] Remove injector air supply hose - note this is a part (035 131 491T) and not just a hose - it has a constrictor inside it
- Using a mirror and "removal grade" Allen drivers, unscrew and remove the inlet manifold - difficult if Dialynx exhaust manifold fitted because of raised lettering cast into manifold. Beware that screws may suddenly release - damage to hands may result. A heavy glove is advised. Otherwise consider removing head with both manifolds attached - assistant required
- Unbolt top water hose from side of head
- [MB, MC, 1B] Detach wire from temperature sender below steering pump
- Remove cam cover and gasket
- Slacken head bolts diagonally from outside inwards, half turn at a time. Head gaskets usually contain a tightening sequence - follow this in reverse
Miscellaneous notes:
- Before-and-after compression tests may be useful - one set with all plugs removed and one set with them in place
- This procedure removes the fuel injection system as a sealed entity apart from opening the feed and return lines and is similar to the procedure recommended by Audi in D 000.5147.00.00 frame 10-5 ff. Although it may seem more convenient to take it off in pieces, this increases the danger of contamination. Whichever approach is used, all open ends should be wrapped in aluminium foil immediately they are detached. The small aluminium shrouds fitted to later injectors are sometimes pulled off when the injector is removed. If this happens the shroud can be recovered on the bench; the injector has three small dots at the end that should just be visible when the shroud is refitted.
- If renovating the head, other components such as injector and injector seat seals, injector tip seals (later engines), valve stem oil seals, etc., may be required. A special spring compressor is required because of the depth of the collets within the head. If the cam cover gasket is replaced, note that some heads have shouldered studs and some do not. Professional head renovation is uneconomic on unmodified MB and MC engines - Audi's exchange heads cost significantly less than the parts and labour and are far superior in performance. Recent deletion of the WR head and substitution with the much more expensive (though almost identical) KG head has unfortunately changed this picture for older 10V engines. If fitting an exchange head, check that all the blanking plates (especially on the back of the head) and temperature sensors are transferred from the used cylinder head before returning it to Audi. Removing the rear blanking plate from an old cylinder head may require impact Allen drivers and considerable care.
- An Audi-supplied exchange cylinder head may differ markedly in appearance from the replaced head. Specifically; there may or may not be a plate covering a hole on the left side of the casting - this is used in North American applications to mount a vacuum pump. MB/MC/1B heads have a mounting hole for a temperature sender below the hydraulic pump bracket - this may or may not open into the water jacket. There may be other minor differences. The part number cast into the side of the head is not meaningful. The head should be tipped to check there are no foreign bodies sitting on top of the valves and spark plugs should be fitted loosely before the head is mated to the block to prevent foreign bodies falling into the engine unnoticed. Various senders and plugs on the rear of the head may need to be transferred - do not release the old head for exchange until the new one has been fitted.
- If fitting a second-hand head, check that all of the threaded holes to be used are in good condition and unobstructed. Repairs such as helicoiling are much cheaper while the head is portable. Helicoils are stronger than the original alloy - any doubtful threads should be treated.
- Reconditioned turbos are sometimes slightly mis-oriented - it may be necessary to loosen the clamping nuts on the "hot" side and rotate the housing to line up the oil, water and air output
- Re-assembly is the reverse of disassembly. Check that the head bolts are correct (e.g., WR 98mm, MB 96mm) and that the bolt holes in the block are free of oil (danger of hydraulic lock). Spin a head bolt fully home into each bolt hole before mating the head to the block.
- Check that both the flywheel and the cam gear are at TDC before mating the head to the block. In the photograph, the crankshaft is deliberately misaligned - it needs to be rotated one or two degrees to bring the mark into the position shown in the diagram. This mark can be VERY hard to find and it should always be painted white if the flywheel is taken off the car.
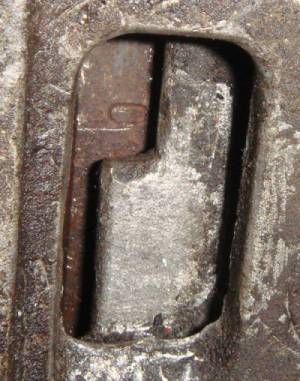
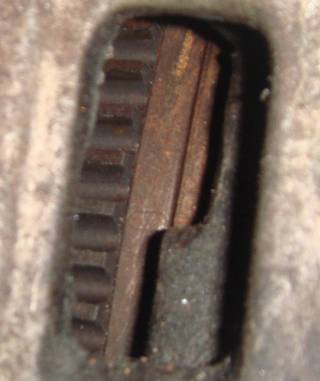
- The wastegate support brackets on the WR engine may be omitted if the right side engine mount is renewed and an appropriate instruction to inspect it 60k miles later is entered in the service record. The full load switch test should be carried out on the WR once re-assembled, since it is easy to fit the idle and full load connectors to the wrong switches.
- It may be appropriate - especially on cars used in high-salt areas such as the North York Moors, East Coast of Scotland (especially Aberdeen), etc., to replace certain fasteners (such as the lower auxiliary radiator nuts) with stainless fasteners. A list of candidates can be found here. Whether or not the engine mount is renewed, the locking nut on the top thread (part # N 022 167 1) should be replaced - it rusts heavily and access is never better than when the turbo is out of the car. The thread should be cleaned thoroughly before the new nut is fitted
- Turn the engine at least once by hand before starting it
- It may be advisable to renew the water pump and/or its seal - they sometimes do not reseal after adjustment. This will usually require removing the cam belt backing plate - if this is done, none of the fasteners should be fully tightened until all are in place. Note that the lower ones also block oilways and oil leaks will result if they are inadequately tightened. If they are overtightened and shear, the engine block must be removed for repairs - observe the torque specifications. Exchange water pumps often come with thicker seals - use the seal supplied with the pump.
- The best test for bent valve stems - cambelt failure, etc. - is to mount the valve stem in a small lathe and rotate it by hand against a dial gauge. Any systemic run-out is a failure and the valve should be replaced. A "quick and dirty" technique in the field is to mount the valve stem in a battery-powered drill and observe the edge or the mirrored mating surface against the light. Once again, suspicion is adequate grounds for replacement.
Special Tools:
- Audi 3036 cam locking tool - a crescent welded to the end of a bar with two pins to lock the cam wheel
- Audi 2084 crank locking tool - not needed if 3036 available - a flat plate locking the crank pulley to the alternator post
- One of the best spanner kits available is the Halfords combination open-ended and ratchet sets - either rigid or flexible. Included in the kit is an Allen bit holder that fits into the 10mm ratchet spanner. This is IDEAL for holding a shortened 6mm Allen bit for the cam belt cover nuts.
- It is much easier to replace the wastegate diaphragm when the wastegate is off the car.
- 12mm triple-square driver for head bolts - NOTE THESE ARE NOT TORX BOLTS. The correct tool can often be found in accessory shops marked for 'VW Head Bolts'. Sometimes it will be packed with two other bits - a 6mmm and an 8mm for halfshaft flange bolts - it may be worth discarding these and cementing or welding the 12mm permanently into the adapter.
- An extra-long ball-end 5mm Allen key, parted off and cemented or welded into a 5mm 1/4" drive socket to yield a driver around 110mm in length. This is ideal for releasing the warmup regulator from the engine block as the oil dipstick tube is somewhat in the way, and is also useful for the cold start valve.
- An extra-long ball-end 6mm Allen key, parted off and cemented or welded into a 6mm 1/4" drive socket to yield a driver exactly 141mm in length. This tool is ideal for accessing the inlet manifold securing screws, especially when a Dialynx manifold is fitted (the raised lettering on top fouls access). It may be useful to wear a heavy or padded glove on the hand applying force - inlet manifold screws release very abruptly and completely. Note that on some engines the front inlet manifold screw cannot be inserted with the manifold in place because it fouls turbo supply lines - it must be inserted before the inlet manifold is offered up to the head.
- The later 10V engine blocks (MC, MB, 1B) have small locating posts for the cylinder head gasket, which are absent on the earlier engines (WR, WX, GV). If working alone on one of the latter, it may be useful to make up equivalents since juggling an assembled head, exhaust manifold and turbo while trying to line up a gasket and drop a bolt through can be frustrating. Grind or cut the heads off two old cylinder head bolts and cut screwdriver slots in the tops. Place these in two of the holes on the block to locate the gasket - lower the head over them and insert other bolts, then remove the locators using the screwdriver slot and a magnetic retrieval tool. The ridiculously rich might obtain two VAG 3070 lead bolts - which are exactly the same thing.
Parts required:
- Cylinder Head Bolts and Washers (x12). Note that some aftermarket and/or grey import head bolts are markedly inferior to original Audi bolts. On all bolts, the thread is M11. On the inferior bolts it is rolled out of an M10 blank - the washer is slid on before the thread is rolled on and is almost captive. Original Audi head bolts are cut out of M11 blanks and the washer is not captive. These bolts are much stronger and also locate the cylinder head more precisely. Part numbers:
- [WR, GV, WX] 049 103 385
- [MB, 1B, MC] 049 103 384B
- 056 103 377 Washers (may come with bolts)
- [WR, GV, WX] 035 103 383J Cylinder Head Gasket
- [MB, 1B, MC] 034 103 383AA Cylinder Head Gasket
- 028 129 589B Exhaust Manifold Gaskets (x5)
- [WR, GV, WX] 034 129 717M Inlet Manifold Gasket
- [MB, 1B, MC] 034 129 717H Inlet Manifold Gasket
- N 901 889 02 Exhaust Studs (x10) - not required with exchange head
- N 900 955 01 Washers (x10, reuse possible)
- N 902 002 01 (Philidas PIL-YZP-M8) Locking Nuts (x10)
- N 012 608 1 Speed Nuts (x10 - not fitted during manufacture, added via TSB)
- 035 129 589D Turbo to exhaust manifold gasket
- 437 253 115 Turbo to downpipe gasket
- 035 145 749 Turbo retaining nuts (x4 - expensive - may be reusable but sometimes must be cut off)
- N 010 244 16 Concertina Pipe Bolt (x3)
- 059 129 601 Locking nut (x3)
- 052 121 091A Gasket for water union
- N 014 711 2 Inlet manifold bolts (x8)
Kerbside Motors Home Page and Contact Information